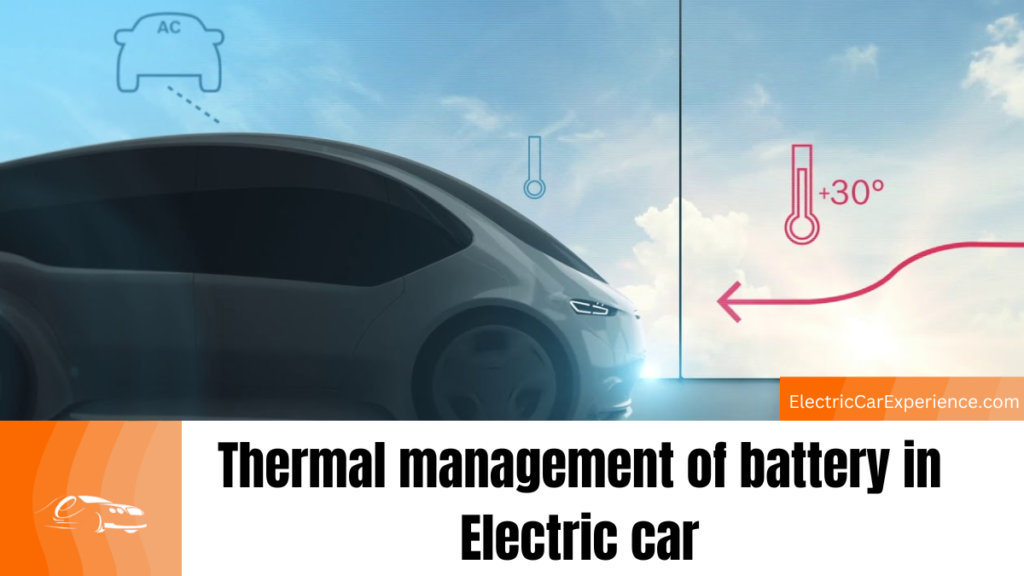
Nowadays, combustion engine vehicles are being replaced by electric vehicles. Increased energy demands and imbalance distribution of energy needs that fossil-based energy resources should be replaced by renewable energy resources. How do the Thermal Management System of Batteries in Electric Cars and Vehicles Work?
That’s why electric vehicles are in demand. Batteries are the source of providing renewable energy to those vehicles. So, for optimizing and monitoring the thermal status of the battery, Battery Thermal Management Systems (BTMS) is generated.
BTMS is a device that allows the battery to operate safely, effectively, and efficiently. It is done by the management of the radiation during the electrochemical processes occurring in the compartments of the battery.
Thermal management of batteries in electric cars is necessary for traditional automobiles to keep the internal combustion engine cool. The engine’s heat is dissipated by the radiator, coolant, and thermostat systems.
Thermal management in electric vehicles comprises cooling the motor, power electronics, and battery systems.
In this article, Let’s examine more closely how thermal energy is produced in the electrical vehicle and why thermal management is so important in electric vehicles.
What is the Thermal Management of Batteries in Electric Cars?
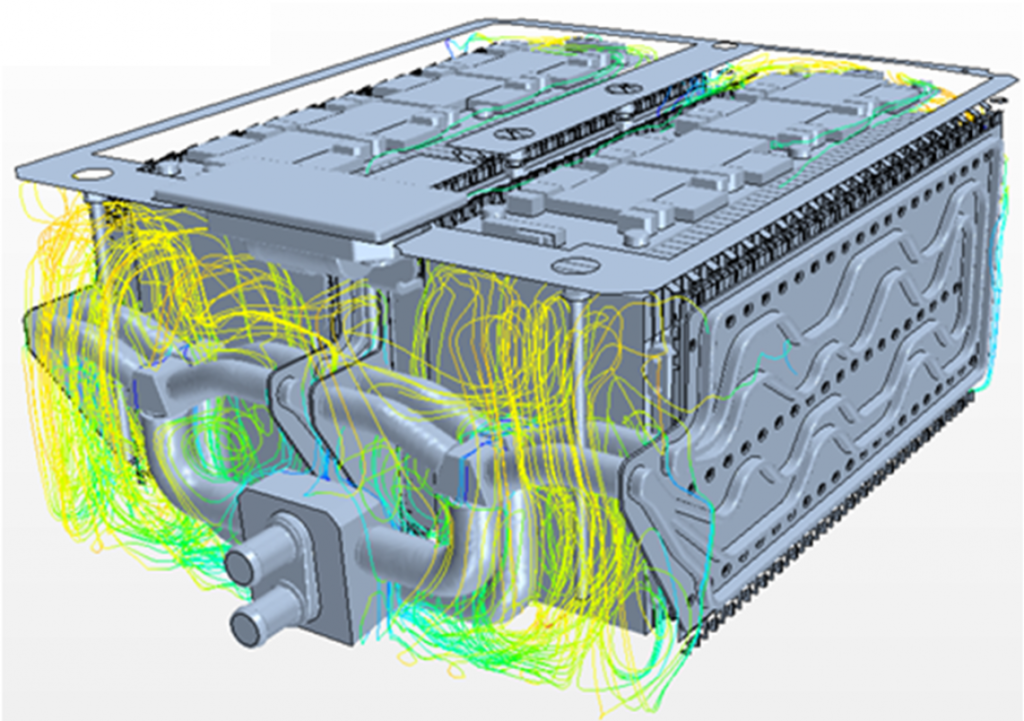
The main purpose of BTMS is the reduction of unequal distribution of temperature (i.e., the temperature will be distributed homogenously in the range of 3C to 4C).
it is necessary to manage the thermal energy of the battery because heat is worse for the car’s engine, as high heat deteriorates the ability of the battery to charge by initiating the chemical reactions which produce gas and certain by-products.
Let’s understand from which parts the heat is radiated and how it is managed.
In the battery of electrical vehicles, heat is generated by the followings:
- The heat generated by the power electronic system
- The heat generated by an electric motor
- Heat radiated by battery packs
- The heat generated by the charger of the battery
- The heat generated by Power Electronic Systems
Electric motor control is handled by power electronic systems. The electric motor is driven in accordance with the control instructions by power electronic systems that work in tandem with the electric vehicle control system.
The power electronic system consists of an onboard charger, inverter, AC-DC rectifier, and DC-to-AC converter. The heat generated by the power electronic circuits while they are operating must be released, and good thermal management is crucial.
To maintain ideal temperatures, the power electronic system is typically coupled to the cooling system of the electric car.
- The heat generated by an Electric motor (e-motor)
The e-motor is one of the vital parts of the electric car, along with the battery pack. Since there is no need to warm up the e-motor when it comes to thermal management, all commercially available solutions focus on cooling the motor’s internal parts.
The e-cooling motor is crucial because a temperature increase greatly reduces the electro-mechanical conversion’s efficiency.
Cooling options for electric motors
When examining the solutions put out by industry players like Volkswagen AG, YASA, or Punch Powertrain NV, there are primarily two cooling options for e-motors.
Use of an exterior cooling jacket on the one hand, and internal cooling through the rotor shaft on the other.
The suggestion is to use liquids as heat transfer fluids in both approaches (water, coolants, or thermal oils).
The fluid used in the other car components will have an impact on the choice of fluid. The requirement to submerge the engine in oil is even thought to be the only way to produce the necessary cooling power in extreme circumstances, such as race vehicles.
- The heat generated by the Charger
Many operating components of the electric car (connections, conduits, power electronics, batteries, etc.) heat up during charging, primarily because of Joule heating.
This means that the power lost during the charging process increases quadratically as the current is delivered.
How to manage Heat Generated by the Charger?
Manufacturers typically advise slow or semi-fast charging to lengthen the battery pack’s lifespan. To reduce recharging times, especially in situations where excursions are longer than the battery pack can handle, the industry is attempting to increase the charging power permitted by the battery.
NAME | POWER (KW) |
Slow | 3, 7 ( AC ) |
Semi-fast | 7,4 ( AC ) – 22 (DC) |
Fast | 50 ( DC ) |
Super – fast | 100 (DC) |
Ultra-fast | 130 – 150 ( DC ) |
Extra – fast | 350 ( DC ) |
Currently, the industry’s biggest problem is developing electrochemical cells that can continuously charge at C-rates of 4 (350 kW of power), which equates to being able to recharge 50% of a vehicle’s range in under 10 minutes.
However, the difficulty lies not only in the electrochemistry of the cell but also in the cooling system needed, as it is predicted that up to 15 kW of cooling power will be needed for exceptionally fast charging.
The automotive industry cites the usage of systems based on immersion in dielectric fluids as the only viable alternative up to this point to address this necessity
- Heat radiated by a Battery pack
The battery pack may need to be heated (in cold locations, before a quick charge, etc.), as opposed to the systems stated above, or cooled (in summer, during fast charges, discharge process, etc.).
This feature makes the overall heat management system more difficult and necessitates efficient component integration.
Additionally, it is anticipated that the introduction of solid-state batteries into the electric vehicle will significantly alter the thermal management needs for this component in the near to medium term.
Solid-state batteries operate at high temperatures (currently around 70 oC, although they are already in the process of reducing it to room temperature), whereas Li-ion batteries with liquid electrolyte (currently used) have an optimum operating temperature between 15 and 35 oC, although they can work outside this range.
Due to the increased thermal demands of this new environment, the battery pack will need supplemental heating systems to function.
BTMS by Cooling Loop in Electric Vehicles
Optimal temperature maintenance is crucial for electric vehicles to operate at a high level of efficiency.
The cooling system of the electric car controls the ideal temperature. The battery pack temperature, power electronic-based drive temperature, and motor temperature are all typically regulated by the cooling system.
The batteries, electronics, motor, and related components are cooled in the cooling loop by a coolant that is pumped by an electric pump. Radiators are utilized in the cooling loop of electric vehicles to discharge heat to the surrounding air.
Evaporators are utilized in electric vehicles to remove heat from the cooling loop and the air conditioning system is used to cool the systems inside the cooling loop.
To maintain the ideal temperatures for battery packs, power electronics drives, and electric motors, thermal management in electric vehicles responds to external-internal temperature circumstances.
Thermal control is essential since it affects an electric vehicle’s safety and drivability.
It is crucial to consider not only the battery pack but also other components such as the electric motor, the cabin temperature control system, the battery charging system, and/or the power electronics when designing a thermal management system in an electric vehicle where driving range is still a challenge.
Thermal Comfort Inside the Cabin
With the internal combustion engine (ICE) gone, an issue that arises in electric vehicles is how to meet the thermal requirement of the cabin to ensure passenger comfort.
This heat is “free” in ICE vehicles since it is produced at high rates and results from engine inefficiencies; the surplus must be vented to the outside.
The amount of heat generated by the EV’s various inefficient parts is substantially lower, and in many cases, it is insufficient to supply the whole need.
In this regard, it is essential to have an additional system that produces the required heat utilizing the energy from the battery.
The most effective method for ensuring the comfort of the passengers in the car is the main concern in this situation.
The use of air to heat the inside as it has been done in the past, heating only surfaces like the seats and steering wheel, etc., or a combination of the two are among the alternatives being investigated.
The simplest and most cost-effective method for using air is to use electric resistances. However, compared to the usage of heat pumps, this approach has low efficiency (more expensive).
By heating only, the regions of the cabin with people, direct surface heating is viewed as an alternative to maximize energy consumption and ensure thermal comfort.
There doesn’t seem to be agreement on a common answer. The current approach in the industry seems to differ for compact vehicles and luxury vehicles nowadays.
The earliest ones, where cutting costs is a top focus, typically come standard with an air-conditioning system based on air heated by resistances and, as an option, provide a heat pump with the goal of reducing power consumption and, as a result, extending the range of the vehicle.
However, in high-end automobiles, a heat pump (air) and the surface heating combo are typically the conventional fixes (seats and steering wheel).
What are the Different Types of Battery Thermal Management Technologies used in EVs?
Active, passive, parallel, series, thermoelectric cooler, and hybrid (phase change material or heat pipes) technologies are used for the management of heat in the battery of electrical cars.
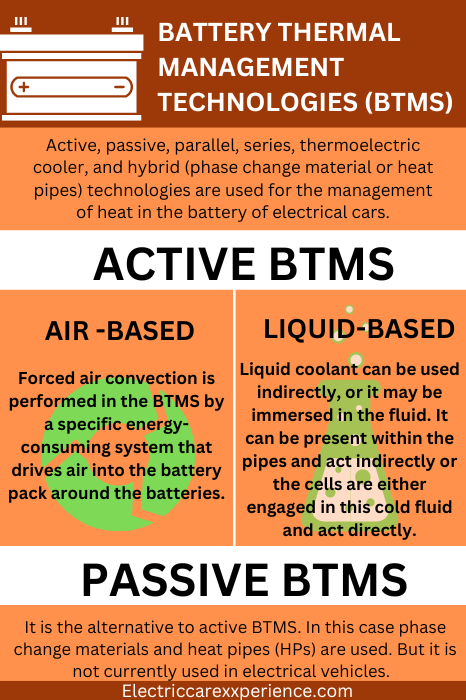
Active BTMS
Air-based BTMS
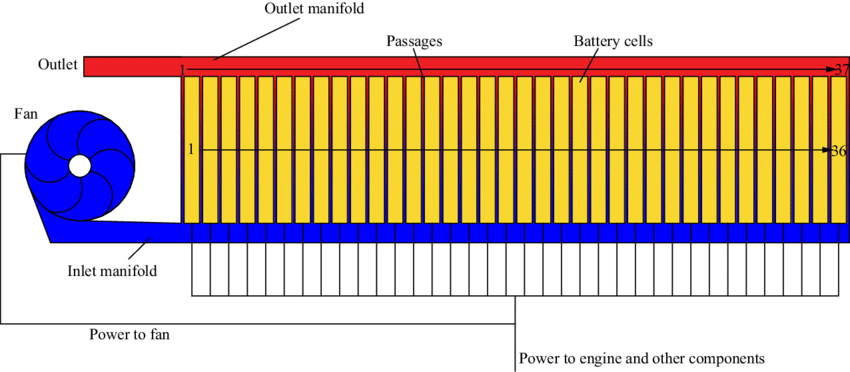
Forced air convection is performed in the BTMS by a specific energy-consuming system that drives air into the battery pack around the batteries.
In BTMS with natural airflow convection, the air is provided to the battery pack spontaneously by convection without the need of additional energy.
Liquid-based BTMS
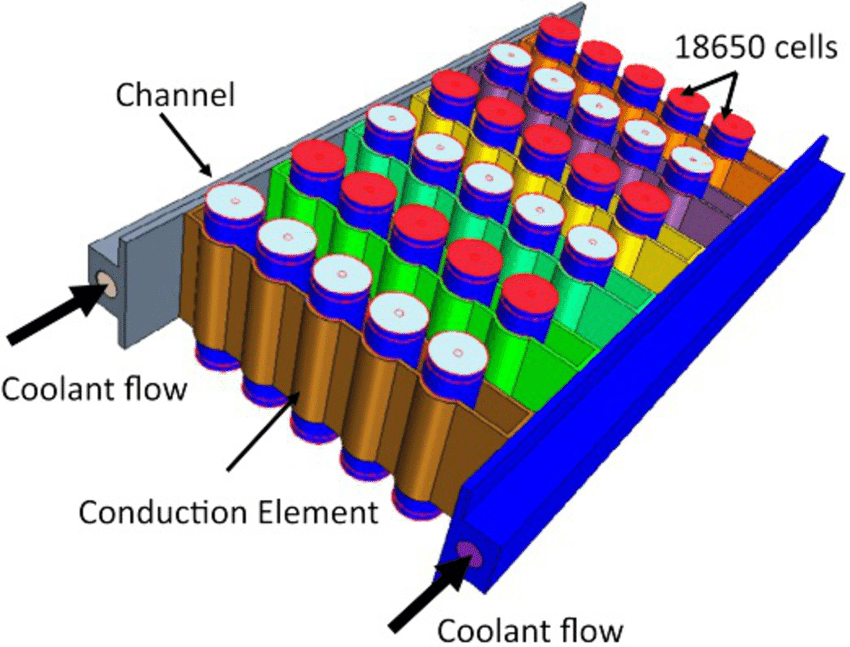
In active BTMS, there is fluid in motion. It is based on forced air. In some cars, fans are used to move or circulate fluid in the battery, and some cars have channels that are in direct contact with the cells in which cool air or fluid (water + ethylene glycol) is circulating.
Liquid coolant can be used indirectly, or it may be immersed in the fluid. It can be present within the pipes and act indirectly or the cells are either engaged in this cold fluid and act directly.
Passive BTMS
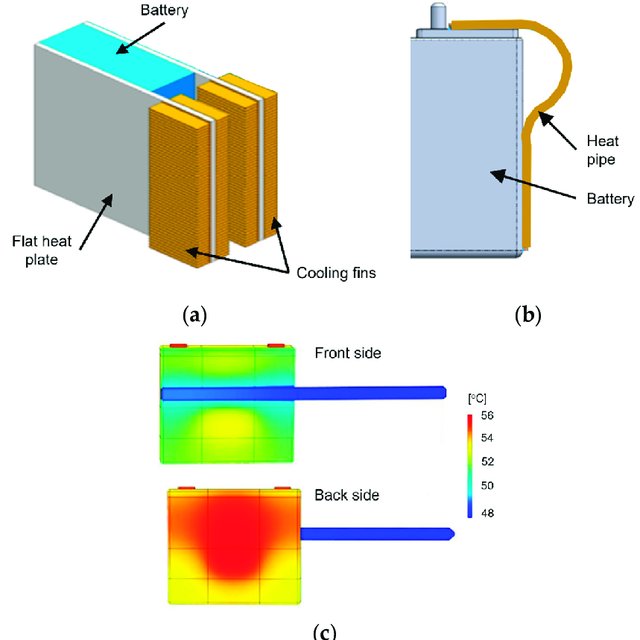
It is the alternative to active BTMS. In this case phase change materials and heat pipes (HPs) are used. But it is not currently used in electrical vehicles.
PCMs, particularly those featuring a solid-liquid phase shift, have been widely researched for use in BTMS. The fascination with these materials stems from the prospect of investigating the high energy associated with phase shifts (usually >150 J/g) that occur at virtually constant temperatures.
These two properties make them appeal when it comes to keeping a consistent temperature throughout the battery pack, near the phase change temperature of the installed PCM.
What is the Role of Thermal Storage in the Future?
The heat storage system is a component that is not currently included in electric vehicles but is expected to play a significant role, particularly when solid-state cells and the potential for extra-fast charging are combined.
Phase change materials (PCMs) are the basis for the thermal storage technology with the greatest benefit for this application, primarily due to their maturity, high energy density, and capacity to supply energy at a constant temperature.
In fact, manufacturers of auto parts like VALEO already sell gadgets of this kind in their catalogs.
FAQS
What is meant by thermal management?
Monitoring and regulating the temperatures that are produced by equipment in electrical enclosures are known as thermal management. Highly technological materials and components with well-known thermodynamic and heat transfer qualities enable control.
What are the basics of thermal energy management?
A thermal management system uses technology to regulate temperature. Thermodynamics and heat transport are the foundation of this technology. Thermal management is a broad phrase that refers to a variety of processes and different types of heat transport, including conduction, convection, and radiation.
What is a battery thermal management system for an electric vehicle?
The battery’s Thermal Management System (BTMS) controls and dissipates heat produced by the electrochemical reactions that take place in the cells and enabling the safe and effective operation of the battery.
What is the function of a thermal system in electric vehicles?
To maintain the ideal temperatures for battery packs, power electronics drives, and electric motors, thermal management in electric vehicles responds to external-internal temperature circumstances. Thermal control is essential since it affects an electric vehicle’s safety and drivability.
Related Posts
- How is a Lithium Crisis Tied to an Inflation Reduction Act?- A complete guide 2024
- Are Electric Car Batteries Harmful to Your Health?
- chevy bolt extended warranty – Latest Updates
- The basics of electric vehicle battery grounding
- How Many Pounds of Raw Materials are Needed to Make an Electric Car Battery
- Tesla Model 3 Error Messages (Error Codes)
- What Kind of Batteries Did Electric Cars Use Before Lithium-Ion?
- Can You Power Your House With Used Electric Car Batteries? If So, Is The Off-Grid System Created From Those Batteries Legal?-An Ultimate guide 2024
- Radiation From Electric Cars
- Are Polyjoule Batteries Fire Resistant?
- Can An Electric Car Battery Be Divide Into 2 Batteries So That You Can Charge Both Of Them At The Same Time And Reduce The Time Of Recharge By Half?
- Nissan Leaf Battery Replacement Cost